Blog 1 (Laser Cutting)
- jylai21
- Nov 5, 2022
- 5 min read
Laser Cutting Documentation Blog Entry
In this page, I will describe:
1. The 4 important hazards associated to the operation of laser cutting machine
and their respective safety control measures (administrative/engineering
control).
2. The materials that can be cut and can’t be cut using laser cutting machine.
3. The steps including pictures on the operation of UNIVERSAL laser cutter, that consist of:
a. Starting the compressor, turning on the laser cutter machine and fume
extractor.
b. Importing a .DXF file to coreldraw and modify the lines/fill for cutting and
engraving.
c. Sending the coreldraw drawing to laser cutter software and setting the
laser cutter power, speed, PPI in the software.
d. Starting the job on the laser cutter machine.
e. DOs and DONTs when there’s flame/fire on the material being cut.
4.My Learning reflection on the laser cutter activities.
1. These are the 4 important hazards and the respective safety control measures on the operation of laser cutting machine:
Hazards | Safety control measures | Pictures to support the explanation |
| Cleaning off debris/dust from the machine If the fire is controllable, it can be put out by blowing it out If the fire is uncontrollable, use a fire extinguisher | ![]() |
2. Staring at the laser during cutting process | Take glances instead of staring to check the cutting process | ![]() |
3. Dirty Focus lens due to accumulation of soot, producing dense smoke or fume | Ensure that the fume extractor is on | ![]() |
4. Lifting the lid of the laser cutter immediately | Wait 1 minute to allow the fume extractor to remove the toxic fume first | ![]() |
2. Below are the materials that can be cut/engraved using laser cutting machine in FabLab.
Material | Photo of Material |
| ![]() |
2. Plywood (Laserply) | ![]() |
3. Cardboard | ![]() |
Below are the materials that can't be cut/engraved using laser cutting machine in Fablab
Material | Photo of material |
| ![]() |
2. Metal | ![]() |
3. Polytetrafluoroethylenes (Teflon) | ![]() |
3. Below are the steps on the operation of UNIVERSAL laser cutter machine in FabLab:
a. Starting the compressor, turning on the laser cutting machine and fume extractor.
Steps and description | Photos to support description |
| ![]() |
2. Switch on the power for light switch | ![]() |
b. Importing a .DXF file to coreldraw and modify the lines/fill for cutting and engraving.
Steps and description | Photos to support the description |
| ![]() |
2. Once imported, choose part of the file where is going to vector cut, engrave or vector engrave based on these following: 1) Vector Cut Pen outline Colour : RGB RED Line Width:Hair line 2) Engrave Fill Colour :RGB GREEN Line Width:NONE 3) Vector Engrave Fill Colour :NONE Line Width :RGB GREEN | ![]() |
3. Once done, click on File > Print | ![]() |
c. Sending the coreldraw drawing to laser cutter software and setting the laser cutter power, speed, PPI in the software.
Steps and description | Photos to support description |
1. Click on Cogwheel icon for settings | ![]() |
2. Universal's Material setting will appear. Click on LOAD to show more material settings | ![]() |
3. Select the presets that matches your material type and thickness and select OPEN | ![]() |
4. Before sending the file to cut, check these following details: POWER: describes the output power of the laser. 100% is maximum power (will cause ugly charring). For dark wood engravings or stamp engravings, you generally need high power,whereas low values are used for materials such as paper. *Ensure power is less than 50% SPEED: describes the movement of the laser head. Fast speeds lead to short exposure times, slow speeds lead to long exposure times. PPI: Pulses Per Inch, Frequency may also be known as PPI or pulses per inch and is a way to control how many times the laser pulses over a given distance during the cutting process. The higher the frequency the more pulses you have and the more they will overlap resulting in a smoother cut, however the downside to this is that the higher the frequency the more heat it creates while cutting which can cause melting orcharring on certain materials. Z-Axis: Usually set as the material height for optimal focus point Check that all colours on the UCP’s Material setting except red and green are skipped Once done, Click OK | ![]() |
If dialog disappear, click on the UCP icon | ![]() |
d. Starting the job on the laser cutter machine.
Steps and description | Photos to support the description |
1. Understanding the Universal Control Panel (UCP)
Under Essential Tools, there are 4 tools to be familiar with. Zoom - Zoom in using the scroll wheel Focus - Check if your work is within the workable space using a laser dot Move - Move drawings within the workable space Estimated time - Determine the estimated time to finish your cut/engrave | ![]() |
2. Open the lid of the laser cutting and place the scrap material provided by FabLab onto the laser cutter | |
3. On the UCP, click on the Power Button to activate the laser cutter on the top right of the control panel. *IF YOU SEE THE PLAY BUTTON IS GREEN BEFORE YOU ACTIVATE THE UCP. PLEASE DEACTIVATE AND REACTIVATE IT AGAIN | ![]() |
4. Using the built-in ruler, check the Horizontal and Vertical sides and with the Universal Control Panel (UCP), click and use the Move tool to move the object to an empty side of the scrap material. | ![]() |
5. With the UCP, click on the focus tool, and a crosshair will appear. With the crosshair, ensure that the file is within the safe cutting area to avoid the object cutting over the voids of the scrap material. Click as close as possible to the extreme bottom right corner of the file | ![]() |
6. Next check the top left corner of the file Check more points if required to make sure the file is within the safe cut zone on the scrap material | |
7. Click on Estimate time Button and press the START button to check for the timing (This does not start the laser cutter) | ![]() |
8. When ready, close the lid gently and press either the PLAY button on UCP or the physical button on the laser cutter | ![]() |
9. Monitor the cut occasionally by glancing at it (DO NOT STARE AT THE BEAM) | ![]() |
10. Once done, wait around 1 minute to let the extractor remove the toxic smell & particles before lifting up the lid. | |
11. Once extraction is done, gently lift up the lid (DO NOT ATTEMPT TO REMOVE MATERIAL YET) | ![]() |
12. Tap on the cut material to see if it's free from its main material. Inform staff in charge if the material didn’t cut through as the laser cutter lens might be dirty. | ![]() |
13. Remove the cut material and gently close the lid | |
14.Shut Down 1. Remove any unwanted materials and dispose them 2. Deactivate the Laser cutter 3. Switch off the necessary switches *Do not need to shut down the PC | |
e. DOs and DONTs when there's flame/fire on the material being cut.
DOs and DONTs | Photos to support the decription |
DOs 1) Any flame MUST DIE OUT within 1-2 seconds. If the flame persists, lift the lid of the laser
cutter and stop the cutting operation.
2) If the fire is negligible, try putting it out by blowing it off
3) If the fire is unable to blow off,
a. remove material from the laser cutter
b. place it on the floor and step on it to put out the fire
4) If the fire is uncontrollable, go to the closest fire extinguisher and put it out. Get people’s
attention by shouting for help.
| ![]() ![]() |
DONTs
| |
4. Below is my Learning Reflection on the laser cutter activities.
It was a enriching and interesting experience for me to learn about the CO2 laser cutter.
During my tutorial lesson with Mr. Chua, he informed us about the practical lesson about operating the laser cutter. I first initial reaction was uncertain as operating the laser cutter was an entirely new experience for me and personally, I do not like to step out of my comfort zone. In addition, when Mr. Chua was going through the slides about the laser cutter. He was talking about the working principle behind the laser cutter, he showed us a YouTube video explaining these working principle. Inside of a large glass tube which is namely filled with CO2 and some Nitrogen, high voltage electricity is passed through the tube which excites the gas particles and produces an invisible beam of high powered laser beam. This laser beam that is exiting the tube will be immediately bounced onto different mirrors and through a focus lens inside of the nozzle which will be ejected onto the working area. Then, the focus lens will focus power of the laser beam down to a single point similarly to when you try to focus a sunlight through a magnifying glass. I also managed to learn about the focal point (point where the power of the beam is the highest) and focal length (the difference between the focal point and focus lens). I found these information quite overwhelming as my knowledge for light is not really good but it was must easier to understand when Mr. Chua explained it in the terms of a magnifying glass, making it easier for me to grasp how the laser cutter worked.
I also managed to learn about which materials can be cut/engraved. These materials are: plywood, natural wood, acrylic, cardboard and paper. Mr. Chua also emphasized on the safety and hazard when operating the laser cutter. He mentioned that when cutting most materials, it can cause small fires and reminded us to be wary of the small fire when operating of the laser cutter. He also mentioned that cutting of PVC or Foam material is not allowed as it produces toxic fumes that contains chlorine. Another important point Mr. Chua mentioned was that if material cannot be cut through, make sure to stop and check if the focus lens is dirty. If its dirty notify and seek assistance from the staff in charge, to allow the lens to be clean. If its not clean it will crack after prolonged use making it unavailable for others to use.
In addition, I learned about Vector and Raster. Vector are digital art that are rendered by a computer using a mathematical formula which consist of anchored dots and connected lines and curves. However, Raster is made up of many tiny pixels which can be noticed and a image is zoomed in. I found this quite interesting as I always thought that all images only consist of raster as all images I have seen is made of pixels, this really surprised me.
Furthermore, I learnt about Corel Draw where we could import our fusion files into the software. From there, depending on whether we want to vector cut, vector engrave (scoring) or engrave, we have to input their own color. For example, like RGB Red and RGB Green. There are other additional tools in Corel Draw to help assist in designing our product.
The last thing we learnt was "Kerf". Kerf is simply the excess material that is removed from the object when it is cut by the laser. Kerf will cut extra material off when it is supposed to fit into something of the correct dimensions. Hence, we have to know of Kerf when doing laser cutting as it can cause inaccuracy in our cut material. So we have to adjust to Kerf, cutting slightly smaller than the desired dimension, by about 0.1 cm to ensure that the Kerf would not affect the cut material.
Before actually doing the laser cutter practical, all of us had to do the FabLab safety quiz which I scored 100% with the power of friendship. But the quiz allowed me to understand the laser cutter in the FabLab much more clearly.
Before operating the laser cutter, Mr. Chua tasked us to create our own Standard Operating Procedure (SOP). Where we were given the universal guide provided on Brightspace to create a SOP, just for me to use. Not going to lie, it was difficult to create one at the start as it is hard to create a SOP without actually doing the laser cutter first. So, most of the time, I spent a lot of time visualizing myself blankly as nothing comes up to my head. But with the help of the pictures provided, I managed to scuff out a decent SOP for me to use in the competency test.
Finally, the moment of truth came, I was the first to start of the competency test, and I felt the pressure as I did not know what to expect. But much to my surprise, operating the laser cutter was much easier than expected. From importing the file to setting the correct engrave/cutting settings to selecting my material settings. It felt like a flow chart where I could follow very easily. But I did make a simple yet fatal mistake. I forgot to turn on the laser cutter on the USP. I think that the pressure of the competency test and Mr. Louis staring at me from the back made me forget. But in the end, with huge amount of luck. I managed to pass the competency test. I also have the a square block with the word "DCHE" engraved as a souvenir. I am proud to say that I am a laser cutter pro now! (Just kidding)
Overall, it was a fun and interesting practical. It really made me step out of my comfort zone and think hard to come out with the step of the SOP. It made me really appreciate the science behind the laser cutter. I hope to use these new skills that I acquired and further improve myself as an individual. I am also excited to use the laser cutting to cut more materials.
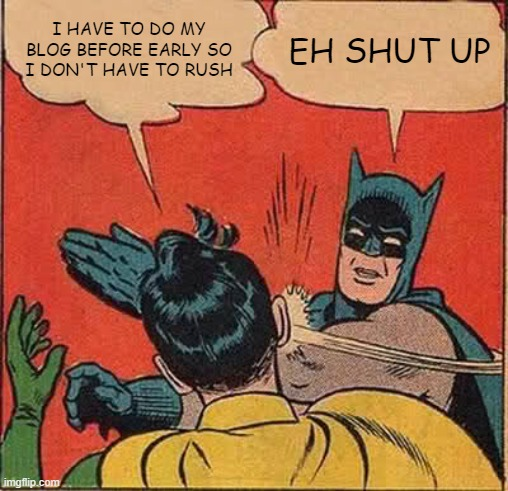
Comments